The Essential Guide to Hydraulic Flanges: Understanding, Choosing, and Using
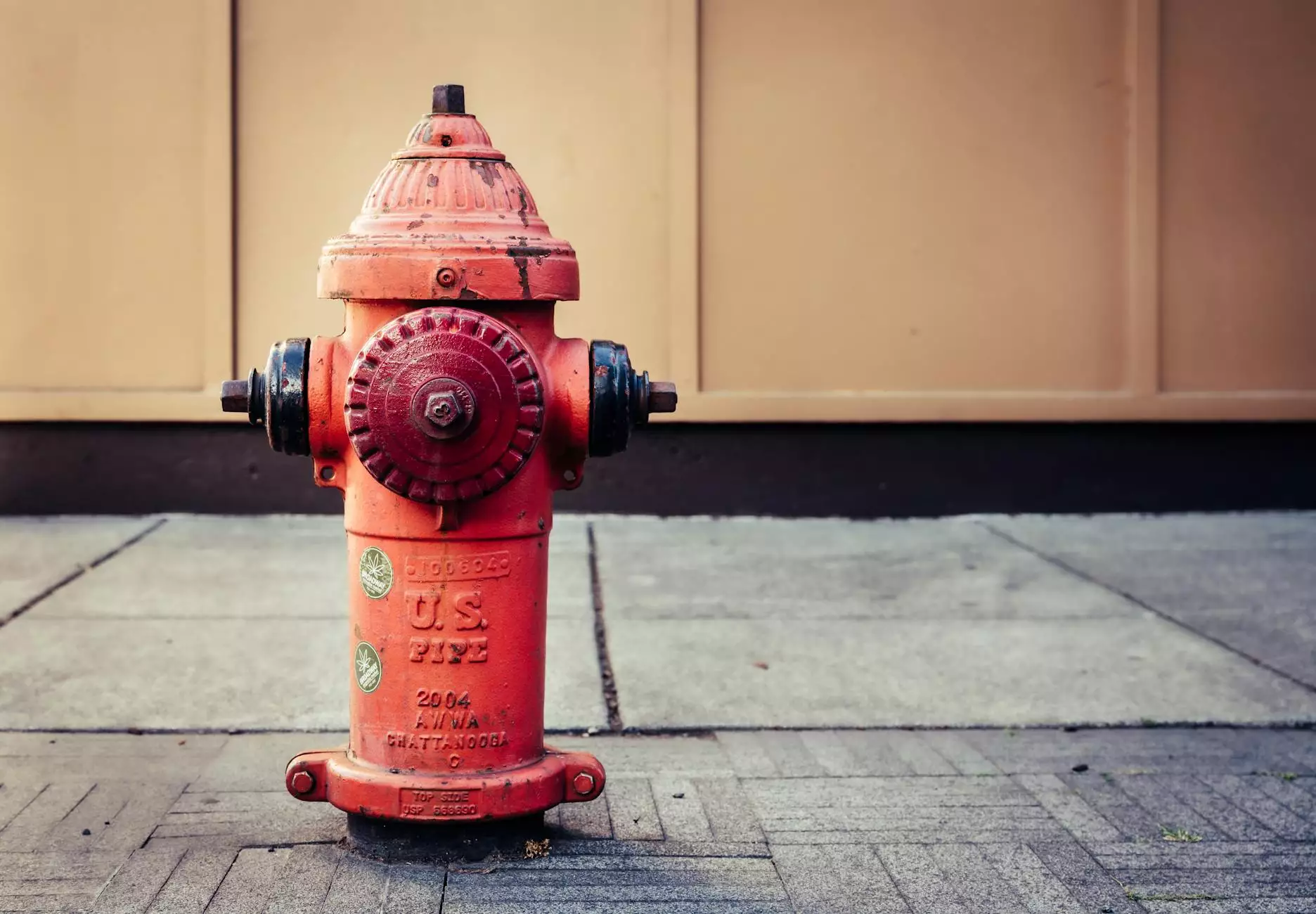
Hydraulic systems are the backbone of many industrial applications, offering reliable and efficient transmission of power through the use of liquid fluid under pressure. Hydraulic flanges are integral components within these systems, providing connections that ensure optimal performance and safety. In this comprehensive guide, we will delve into the intricacies of hydraulic flanges, including their types, specifications, applications, and best practices for selection and usage.
What Are Hydraulic Flanges?
Hydraulic flanges are flat pieces of metal, typically circular or rectangular in shape, that are used to connect two sections of piping in hydraulic systems. They create a tight and secure joint, preventing fluid leaks and ensuring that the system operates smoothly. The choice of flanges plays a critical role in the efficiency and functional integrity of hydraulic systems.
Types of Hydraulic Flanges
Understanding the various types of hydraulic flanges can help you make informed decisions when selecting components for your hydraulic systems. Here are the most commonly used types:
- Standard Flanges: These flanges are designed according to established standards such as ANSI, ASME, or ISO. They are widely used due to their availability and compatibility with various fittings.
- Weld Neck Flanges: Ideal for high-pressure applications, these flanges have a long tapered neck that can be welded to the pipe, providing additional strength.
- Slip-On Flanges: These flanges slip over the pipe and are welded in place, making them simpler and quicker to install.
- Blind Flanges: Used to seal off the end of a piping system, blind flanges are perfect for preventing flow through an opening.
- Socket Weld Flanges: Designed for small diameter piping, these flanges are inserted into a pipe and then welded, ensuring a strong joint.
- Lap Joint Flanges: These flanges consist of two components - the flange itself and a stub end, allowing for easy disassembly.
Specifications to Consider
When selecting hydraulic flanges, there are several key specifications to consider:
1. Material
The material of the flange is crucial as it affects durability and resistance to corrosion. Common materials include:
- Carbon Steel: Economical and strong, suitable for various hydraulic applications.
- Stainless Steel: Provides excellent resistance to corrosion, ideal for challenging environments.
- Alloys: Specialized alloys can be used for high-performance applications.
2. Size
The size of the flange must match that of the pipe it connects. Flanges are available in various diameters and thicknesses.
3. Pressure Rating
Hydraulic flanges come with different pressure ratings, typically measured in pounds per square inch (PSI). Always ensure that the flange you choose can withstand the operational pressures of your system.
4. Standards Compliance
Flanges should comply with industry standards to ensure compatibility and safety. Familiarize yourself with the relevant standards for your specific application.
Applications of Hydraulic Flanges
Hydraulic flanges find applications in various industries, including:
- Aerospace: Used in hydraulic systems for aircraft, providing safety and reliability.
- Automotive: Essential in hydraulic braking and power steering systems.
- Construction: Employed in heavy machinery to facilitate powerful hydraulic operations.
- Marine: Used in ships for steering systems and hydraulic controls.
- Oil & Gas: Critical for transporting fluids safely and effectively in exploration and production.
Choosing the Right Hydraulic Flange
Choosing the right hydraulic flange is paramount for ensuring the efficiency and safety of your hydraulic systems. Here are some expert tips to guide your selection:
1. Assess System Requirements
Analyze the specific requirements of your hydraulic system. Consider parameters such as pressure ratings, fluid type, and temperature conditions. This will help you select a flange that is congruent with your operational parameters.
2. Consult with Experts
If you're uncertain about which hydraulic flanges to use, consult with fluid power specialists or suppliers like fitsch.cn. They can provide insights and recommendations based on your needs.
3. Evaluate Quality
Opt for flanges that meet or exceed industry standards. High-quality flanges are less likely to fail, reducing maintenance costs and enhancing reliability.
Installation and Maintenance of Hydraulic Flanges
Proper installation and maintenance of hydraulic flanges are critical to maintaining system performance and safety. Here are some guidelines:
1. Installation Practices
- Ensure that surfaces are clean and free from debris before installing the flange.
- Use the right gasket material suitable for the fluid and temperature conditions.
- Tighten bolts evenly in a crisscross pattern to achieve an even seal.
- Verify that the alignment of the flanges is correct to prevent stress.
2. Regular Inspections
Conduct regular inspections of hydraulic flanges to check for signs of wear, corrosion, or leakage. Early detection of issues can prevent catastrophic failures.
3. Replace as Needed
If a flange shows signs of fatigue or damage, it is crucial to replace it immediately to maintain system integrity.
Conclusion
Hydraulic flanges are more than just simple connectors; they are critical components that can significantly influence the performance and safety of hydraulic systems. Understanding the types, specifications, applications, and best practices for choosing and maintaining hydraulic flanges will empower you to make informed decisions. For high-quality fittings, including hydraulic flanges, remember to explore offerings from fitsch.cn, where you can find premium products tailored to your hydraulic needs.
By leveraging the insights provided in this guide, you can ensure that your hydraulic systems operate at peak efficiency and reliability, thereby enhancing productivity and safety across various applications.